Mastering Molds: Unleashing the Power of Injection Molding
Welcome to the world of injection molding, where molds play a crucial role in shaping not just products, but entire industries. From automotive parts to household appliances, molds are the unsung heroes behind the seamless production of countless everyday items. These precision-engineered tools are the cornerstone of the injection molding process, enabling manufacturers to create consistently high-quality products in a cost-effective and efficient manner.
The intricate design and construction of molds for injection molding are a testament to the intersection of artistry and engineering. Every curve, every cavity, and every detail of a mold is meticulously crafted to ensure optimal product output with minimal waste. With advances in technology and materials, today's molds are more durable, versatile, and precise than ever before, allowing manufacturers to push the boundaries of what is possible in product design and development.
Types of Molds
There are various types of molds used in injection molding processes, each serving specific purposes in creating diverse products. One common type is the two-plate mold, which consists of two plates that separate to allow for easy ejection of the molded part. Another common type is the hot runner mold, which helps minimize material waste by keeping the runner system hot throughout the injection process. Additionally, complex parts with intricate designs often require the use of multi-cavity molds to produce multiple parts in a single cycle.
Design Considerations
When it comes to molds for injection molding, meticulous attention to detail is crucial in the design phase. The geometry of the mold plays a significant role in ensuring consistent and high-quality production output. Factors such as part complexity, wall thickness, and undercuts need to be carefully considered to achieve desired results.
Another important consideration is material selection for the mold. Different materials offer varying levels of durability, thermal conductivity, and resistance to wear. Choosing the right material based on the specific requirements of the injection molding process can greatly impact the overall performance and longevity of the mold.
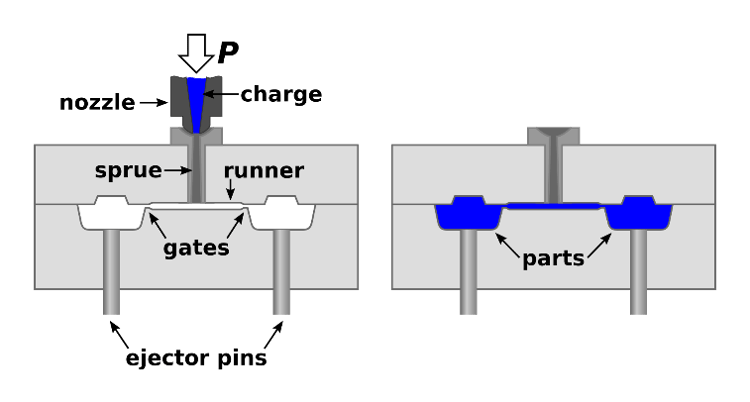
Moreover, gating and venting design are essential aspects that cannot be overlooked. Proper gating helps in controlling the flow of molten material into the mold cavity, ensuring uniform filling and reducing the risk of defects. Similarly, effective venting helps in releasing trapped air or gases during the molding process, preventing imperfections in the final product.
Troubleshooting Tips
One common issue that may arise when working with molds for injection molding is a poor surface finish on the final product. This can be caused by factors such as mold temperature, injection speed, or the quality of the mold itself. To address this, ensure the mold is properly maintained and cleaned regularly to prevent any imperfections during the molding process.
Another potential problem to watch out for is the presence of air pockets or voids in the molded part. This can occur if the mold is not properly vented, leading to trapped air during the injection process. To fix this, inspect the mold for any blockages or areas that may need additional venting to allow for proper air escape and prevent defects in the final product.
Lastly, inconsistent part dimensions can be a frustrating issue when using molds for injection molding . This can be caused by variations in the cooling process, injection pressure, or mold alignment. To tackle this problem, ensure that the mold is properly set up and calibrated, and consistently monitor and adjust the injection parameters to achieve uniform part dimensions.